The Anvil: The Heart and Soul of Blacksmithing
In the world of blacksmithing, the anvil stands as an iconic symbol of craftsmanship and tradition. It is a timeless tool that has been instrumental in shaping metal for centuries.
Join us as we delve into the significance and enduring legacy of the anvil in the art of blacksmithing.
Origins and Evolution:
The origins of the anvil can be traced back to ancient civilizations, where rudimentary stone anvils were used to shape metal. As metalworking techniques advanced, so did the design of the anvil. Today, blacksmiths rely on iron and steel anvils, carefully crafted to withstand the intense forces exerted during forging. The anvil's distinctive shape, with a flat face, a horn, and strategically placed holes, allows for versatile workholding and precise metal shaping.
Anatomy of an Anvil:
To understand the anvil's functionality, it's essential to explore its different parts. The face, typically made of hardened steel, provides a smooth and durable working surface for hammer strikes. The horn, a curved extension, allows for bending, shaping, and drawing out metal. The hardy hole accommodates various specialized tools, such as hardy tools and swages, for specific tasks. The pritchel hole offers a convenient means for punching holes in the metal. Together, these elements create a well-rounded tool that meets the diverse needs of blacksmithing.
Choosing the Right Anvil:
Selecting the right anvil is crucial for any blacksmith. Considerations such as weight, material, rebound, and condition play a significant role in decision-making. While traditional wrought iron anvils possess historical charm, modern options made of high-quality cast or forged steel offer durability and superior performance. Vintage or antique anvils can also be sought after, but it's important to evaluate their condition and suitability for specific work requirements.
Care and Maintenance:
To prolong the life of an anvil, proper care and maintenance are essential. Regular cleaning and removal of scale or debris, along with periodic lubrication, help prevent rust and keep the anvil in optimal condition. Maintaining the smoothness of the anvil face is critical, as any dents or deformations can affect the quality of the work. If wear or damage occurs, techniques such as dressing the face or refinishing can restore its functionality.
Anvil Legends and Lore:
Throughout history, anvils have become woven into folklore and legends. They have been associated with strength, protection, and even supernatural powers. In various cultures, the anvil holds symbolic importance, representing the foundation of craftsmanship and the transformation of raw materials into artistry. These mythical associations add to the allure and reverence surrounding this venerable tool.
The anvil is more than just a tool; it is the heart and soul of the blacksmith's craft. It embodies tradition, craftsmanship, and the dedication of artisans throughout history. Drakon Forge celebrates the legacy of the anvil and its role in shaping extraordinary works of art. Whether you are an experienced blacksmith or an aspiring one, the anvil remains an indispensable companion on your journey of creativity and mastery.
Embrace the power and significance of the anvil as you forge your own path in the world of blacksmithing, and let it inspire you to create masterpieces that stand the test of time.
#TheAnvil #BlacksmithingLegacy #CraftsmanshipUnleashed
Share
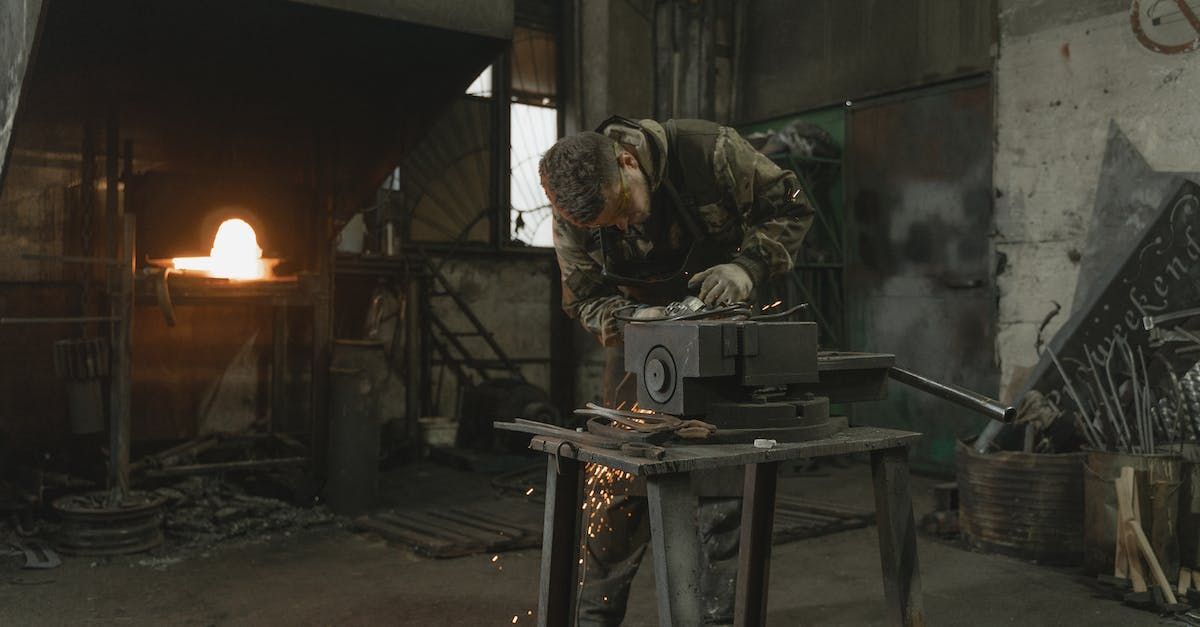